MAS PZターンpzturn
高剛性・高精度 旋盤用クイックチェンジバイト
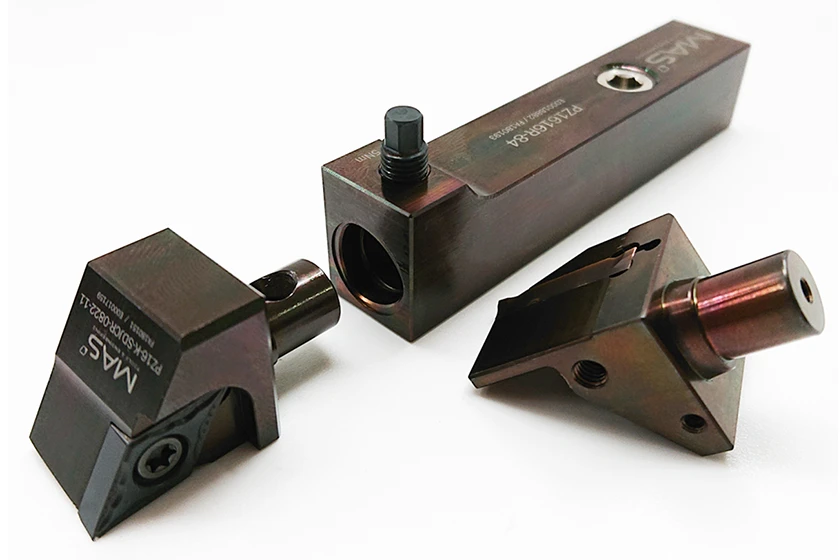
MAS PZターンとは
次のような自動盤ユーザー様にオススメしたいアイテムです
-
人手不足・作業者の熟練度の差がある
-
生産性を上げたい
-
試削りによる不良流出を防ぎたい
-
作業環境を良くしたい
PZターンはくし刃自動盤向けに開発されたヘッド分割式のバイトです。
高精度・高剛性と分割式バイトの常識を打ち破り自動盤の世界で機外段取りを可能にした画期的な製品です。
2018年の国内販売開始から日々ラインナップが拡充され、より使いやすく進化し続けています
PZターンの導入で自動盤の現場が楽になる!生産性が向上する!
- 人手不足の解消
- 新入社員も今日からマイスター
- 変量多品種生産への対応力
- 圧倒的な生産性の向上
- ツール交換が手間でなくなる
- 段取り時間の削減
- だれでも同じ作業ができる
- 一発良品を実現
- もうボルトもチップも設備の中に落とさない
PZターンの特徴
PZターンはテーパーポリゴンカップリング接続が最大の特徴です。これにより一体式ホルダと同等の剛性と高い繰り返し精度を実現しています。
-
1
ヘッドとシャンクがセパレート構造
-
2
ヘッド交換はボルト一本で簡単に交換可能
-
3
トルクドライバーでの脱着で作業の個人差が出にくい
-
4
テーパーポリゴンカップリングで 10μ 以下のヘッド着座位置の繰り返し精度を実現
-
5
セパレート構造にもかかわらず、一体式ホルダの 97 %の背分力抵抗値の高剛性
-
6
PZターンは全てクーラントスルー対応
-
7
シャンクのクーラント接続は 3 箇所対応で様々な取付に対応
-
8
シャンクは設備から取り外さないのでホース脱着が不要
-
9
ISOチップに対応しており各メーカのインサートが使用可能
導入効果
導入効果は様々ありますが【機外段取りによる1発良品】の実現が大きなメリットです。 試削りをなくすことで生産性向上はもちろん、【試削りによる不良品の流出】を防ぐことができます。
-
1
工具交換に伴う設備停止時間を大幅短縮
-
2
『 機外段取り 』の実現
加工機外でヘッドにチップを取り付け、チップの誤差を測定しておくことで補正値を事前計測ヘッドを交換したら即設備を再稼働! -
3
チップ交換後に補正・試削りが不要なので不良品流出原因を排除できる『 一発良品 』を実現
-
4
段取り替えが容易なので、変量多品種生産への対応力が向上
-
5
段取り時の面倒なホース付け外し作業をゼロに
コストメリット
- 生産性向上によるコストメリット
- 人件費削減によるコストメリット
- ボルト紛失削減によるコストメリット
- 試削りによる不良品流出時の損害防止のメリット
PZターンは一般的なホルダより高額になりますが、上記に加えて機内作業が容易になることでのオペレーターの負担軽減となり、昨今問題になっている、新しく社員を雇ってもすぐやめてしまい採用コストが激増&人手不足の悪循環問題のリスクを多少減らせるかもしれません。
人手不足の製造業においてオペレーターの負担をいかに減らし、作業を平準化することが今後のキーとなると考えます。 イニシャルコストがかかるかもしれませんがバイトを交換するだけの簡単改善活動なので早目に導入検討されることをオススメします。
導入実績
いち早くPZターンを導入された国内ユーザー様は非常に大きな成果をあげています。 自動盤加工の世界において【機外段取り】を導入する効果は高いようです。
事例1 栃木県 A社
工程替え段取り作業
段取り時間
60%減
ツールの入れ替え本数が非常に多い製品段取り替え、ホース付け外し、クサビ付け外し、補正など作業量が多く、今まではチップのメーカー毎にホルダーも交換していた。PZターンにすることでホースの付け外しもクサビの付け外しも作業自体が無くなり、ヘッドの着座精度が良いので補正作業も1回で完了するようになった。 また、PZターンを導入することでISO基準のチップに統一。各メーカの優れたチップ(コーティングやブレーカー)をより抜いて選定してもホルダの取り合いを考える煩わしさが無くなった。
これらの多くの改善が積み重なり、平均で1時間40分かかっていた段取り作業が、今では40分以内に収まるようになった。
事例2 大阪府 B社
初めての自動盤導入
1年間のボルト紛失数
0本
初めて自動盤を導入した。小型設備に慣れた作業者はいない状態で生産ラインを立ち上げた。
PZターンの段取り性の良さが貢献し、熟練作業者でも避けられないボルトやチップの紛失を1年間にわたりゼロで運用できた。
事例3 愛知県 C社
部品
寸法の振れ幅
70%減
期間工も多く、人の入れ替わりが多い量産現場。精密部品を加工しているが、どうしても工具の取り付け、補正値の取り方の個人差があり、寸法の振れを抑えられなかった。
PZターンを導入してからは、機外段取りでチップ誤差を測定。試削→補正の工程をやめ、測定値のデータを入力するだけにしたので個人差はほぼなくなり、いままで70μあった外径寸法振れが20μ以下で安定した。
導入事例
下記事例は弊社のユーザー様での実績をもとにした試算です。 1日のチップ交換回数が多い難削材加工をされているユーザー様や、段取り替えの多い変量多品種生産のユーザー様ほど効果が高い傾向があります。
交換作業時間の削減効果
下記はPZ ターンの導入によって従来は1日2回、1回あたり600秒かかっていたチップ交換作業を120秒に短縮できたユーザの事例です。 この場合のチップ交換作業とは設備を停止してからチップ交換を行い、試し削りによる x/z の原点チェックを行い、設備を再稼働させるまでの時間です。
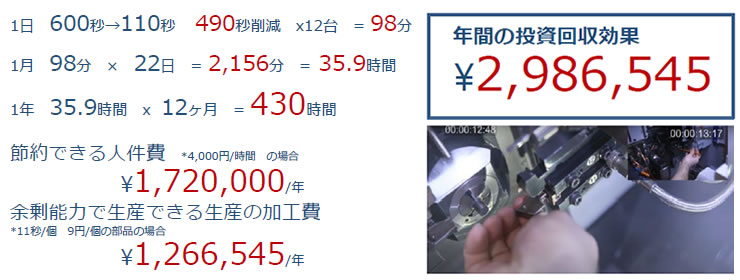
あまり効果が出ないケース
- 刃具交換頻度がすくない(例:1週間に1回程度)
- 試削りや原点だしをしていない
- ワーク加工原価が安い(例:1円未満)
上記はコストメリットだけで判断していますが、上述した作業環境改善や作業平準化を含むと効果が出ないわけではありません。
商品ラインナップ
PZターンはISOインサートに標準対応しており、専用のインサートを使う必要がありません。 現在使用しているインサートがそのまま使用可能です。ヘッドは随時ラインナップを拡充しております。
PZターンは自動盤に最適な10□、12□、16□のシャンクサイズをラインナップ。
PZターンのヘッドは、ISO規格の各メーカー製インサートを使用できる豊富な形式を100種近くラインナップしています。

下記ダウンロードリンクにはより詳しい情報とラインナップが記載されたカタログをダウンロードできます。
カタログダウンロード
ご相談、お問合せはこちら
フォームが表示されるまでしばらくお待ち下さい。
恐れ入りますが、しばらくお待ちいただいてもフォームが表示されない場合は、こちらまでお問い合わせください。